Discover the most up to date Advancements in Metal Stamping for Accuracy Production
Discover the most up to date Advancements in Metal Stamping for Accuracy Production
Blog Article
Discovering the World of Steel Stamping: From Layout to Production
Within the realm of manufacturing, metal stamping sticks out as a specific and efficient approach for forming metal sheets into various forms with amazing consistency. From the preliminary style phase where elaborate patterns form to the complex manufacturing procedures, steel marking is a blend of creativity and engineering. Exploring this world unveils a complex interaction of creative thinking and technological proficiency, supplying a glance right into a realm where development meets craftsmanship.
History of Steel Stamping
Steel marking, a commonly used manufacturing process today, has a rich background that goes back to old times (Metal Stamping). The origins of metal marking can be mapped to ancient worlds such as the Egyptians, that utilized stamping techniques to adorn precious jewelry and accessories with elaborate designs. Over time, steel stamping progressed, with worlds like the Greeks and Romans utilizing it for developing coins and ornamental items

In the 20th century, metal marking remained to advance with the combination of automation and computer system numerical control (CNC) technology. These improvements better boosted the efficiency and accuracy of steel stamping procedures, making it a vital part of contemporary production across markets such as automotive, aerospace, and electronic devices. Today, metal stamping continues to be an important production process, integrating practice with development to fulfill the needs of a regularly developing sector.
Design Factors To Consider and Prototyping
When developing metal marking tasks, precise interest to design considerations and prototyping is essential for making sure optimum manufacturing outcomes. Style factors to consider in steel stamping include material choice, component geometry, tooling design, and production expediency. navigate to this site Picking the right material is vital as it influences the component's performance, cost, and manufacturability. Part geometry influences the complexity of the marking procedure and the capability of the end product. Tooling design plays a substantial role in the success of metal stamping projects, affecting part accuracy, tool longevity, and production effectiveness.
Prototyping is a vital stage in the metal marking process that allows designers to evaluate the layout, verify manufacturability, and make necessary changes before major production. By carefully taking into consideration design facets and utilizing prototyping, suppliers can improve the steel stamping procedure and accomplish premium, cost-efficient manufacturing outcomes.
Tooling and Devices Essentials
Taking dig this into consideration the essential duty that tooling layout plays in the success of steel marking jobs, comprehending the necessary devices and devices required is critical for achieving efficient production end results. Components hold the steel in location during the stamping procedure, making certain precision and repeatability. Spending in premium tooling and devices not only boosts manufacturing performance but likewise leads to higher precision, lowered waste, and general expense savings in steel marking procedures.
Production Process and Top Quality Control
Effectively managing the production procedure and carrying out robust top quality control actions are important for guaranteeing the success of metal stamping jobs. The manufacturing procedure in metal stamping entails a collection of steps that need to be carefully collaborated to attain optimal results.
Quality control in metal stamping is extremely important to supply items that satisfy the required requirements. By preserving strict quality control criteria, makers can support their credibility for delivering high-grade steel stamped items.
Applications and Market Insights
In the world of steel stamping, the successful application of manufacturing processes and quality control procedures directly affects the effectiveness and reliability of pop over to these guys numerous industry applications and gives useful insights right into the industry's operational characteristics. Metal marking finds prevalent application across diverse sectors, including automotive, aerospace, electronic devices, and appliances. In the auto industry, steel stamping plays a crucial duty in generating components such as framework, brackets, and architectural get rid of high precision and performance. The aerospace market relies upon metal marking for manufacturing complex components like panels, braces, and installations that meet rigid quality requirements (Metal Stamping). In the electronic devices industry, metal marking is used to produce specific components like ports, terminals, and warmth sinks. Additionally, metal marking facilitates the production of different house appliances, including refrigerators, cleaning equipments, and ovens, by supplying cost-efficient solutions for producing sturdy and intricate parts. Comprehending the applications and sector understandings of metal stamping is vital for maximizing manufacturing procedures and enhancing product quality across different markets.
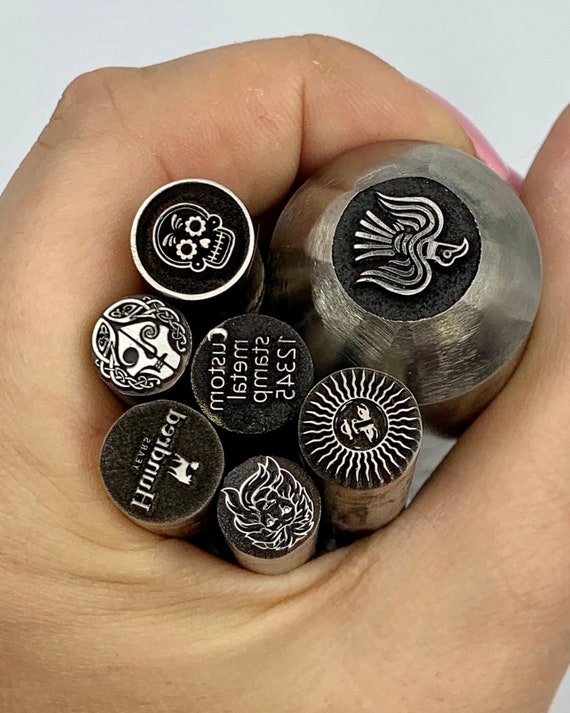
Conclusion
Style considerations, prototyping, tooling, tools, manufacturing processes, and top quality control are vital facets of metal marking. With its widespread applications and sector insights, steel marking continues to be a versatile and reliable manufacturing process.
Report this page